Audit
We perform audits of compressed air systems according to the customer’s needs and wishes. In order to save on compressed air and electricity bills, it is wise to audit your equipment from time to time. It is reasonable to order an audit in companies where the compressed air pipeline is older than 5 years and the equipment has been in operation for more than 3 years. Piping leaks can occur during this time and it is a good time to inspect the system and, if necessary, readjust. Depending on the system and the type of audit, the audit can take twenty minutes or a few weeks.
An audit may consist of all or parts of the following activities:
- measurement of compressed air consumption
- dew point measurement
- pressure measurement
- measuring the electricity consumption of devices
- leak detection
What happens next?
As a result of measuring the parameters, we provide the customer with proposals for improving or rebuilding the system. Sometimes all it takes is relocating equipment or installing thicker piping/a larger tank to achieve significant savings.
Compressed air is a convenient but very expensive form of energy. Almost 75-80% of the costs of an average compressor station is the price of electricity. It would be very reasonable and economically expedient to use all saving options, such as a compressor with a frequency converter, which can save up to 30-35%, or using warm cooling air for room heating.
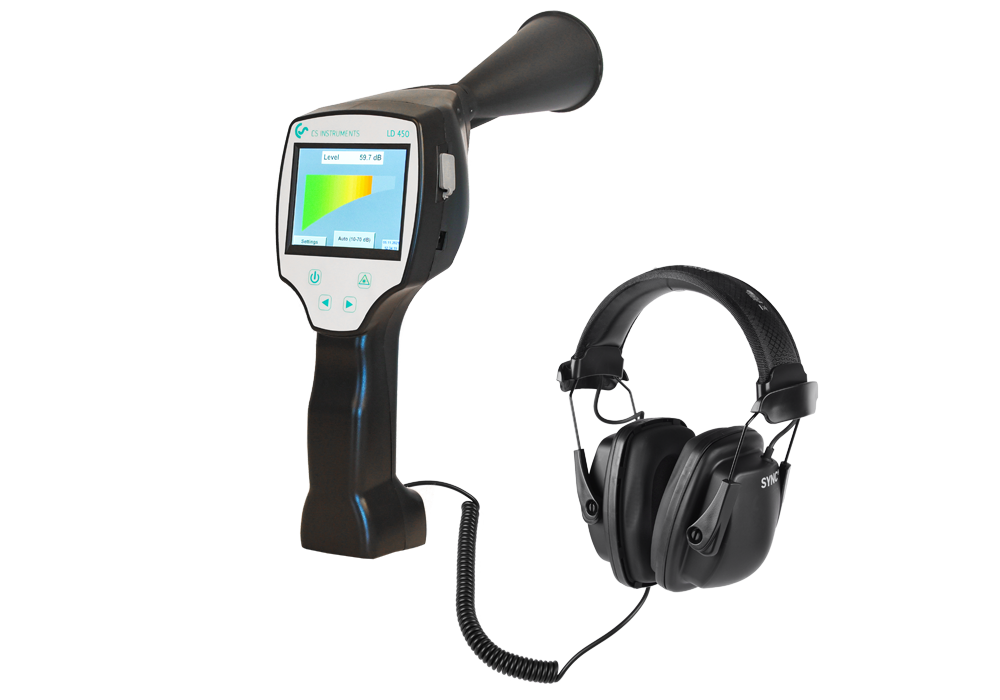
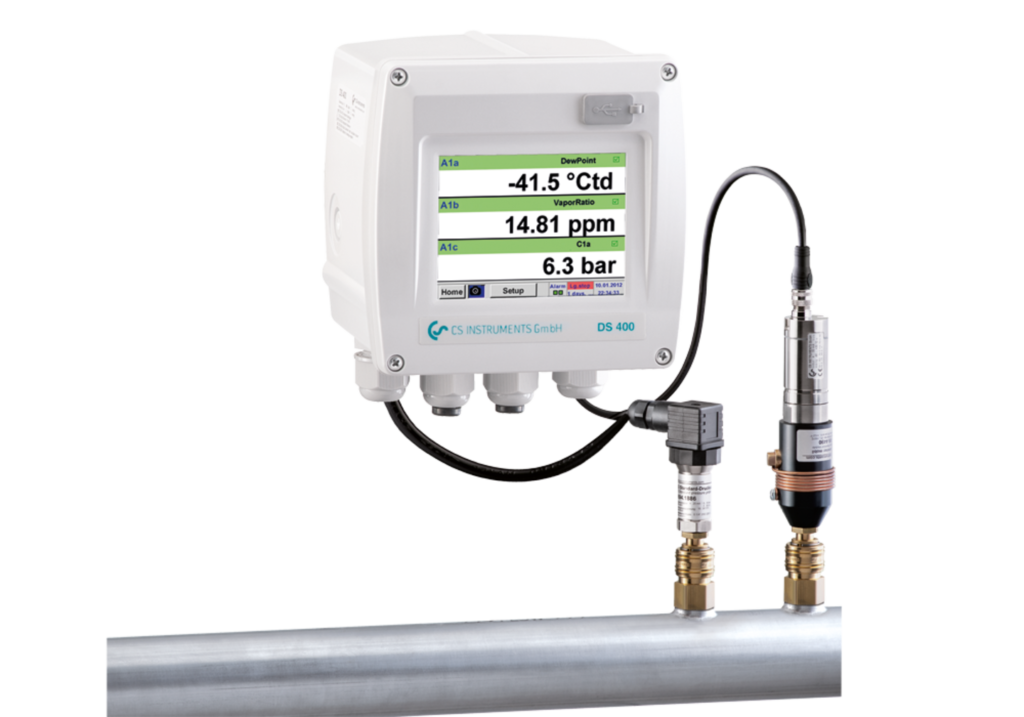
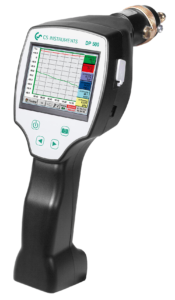